Spółka Wikpol, z siedzibą w Konopnicy w województwie lubelskim, zajmuje się wytwarzaniem zrobotyzowanych linii paletyzacji i pakowania. Firma, we współpracy z Siemensem, wdrożyła technologię cyfrowego bliźniaka. Przedsiębiorstwa wykorzystały digital twin, m.in. do zaprojektowania transportera będącego częścią linii kompletującej torebki makaronu. Jarosław Strug, główny automatyk programista w Wikpolu, wyjaśnia, że celem urządzenia jest ciągłe przechwytywanie produktów bez ryzyka zderzenia się komór odbiorczych mimo dużej prędkości. Trudności w przedsięwzięciu wiązały się z różnymi rodzajami pakowanych elementów, a także potrzebą zachowania efektywności sięgającej 2 torebek na sekundę. Testowanie zabezpieczeń, sterowania układu, a także parametrów urządzenia było możliwe dzięki modelowi cyfrowego bliźniaka współpracującego z programem sterującym.
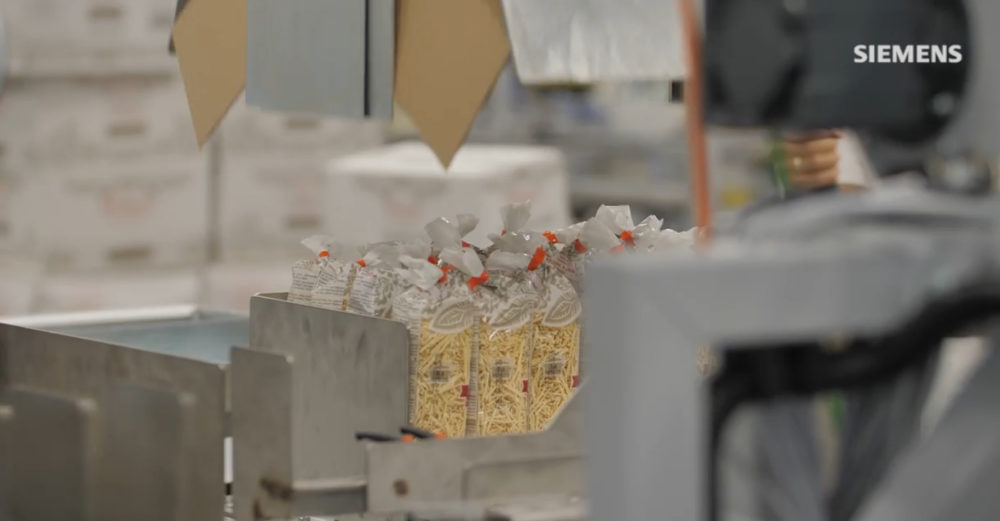
Wykorzystane oprogramowanie
Modele są opracowywane na komputerze klasy przemysłowej z platformą projektową systemów automatyki przemysłowej TIA Portal, wirtualnym sterownikiem PLCSIM Advanced, modułem Mechatronics Concept Designer opartym na systemie NX, który pozwala wykorzystać modele CAD w analizie działania projektowanej maszyny, a także software’em SIMIT do przygotowywania cyfrowych odwzorowań instalacji:
– Dodatek SIMIT, zawierający zintegrowaną bibliotekę obsługującą telegram 105 pozwolił nam na symulacje napędów V90. Dzięki niemu byliśmy w stanie testować kompletny program sterujący zawierający pełny hardware wraz z funkcjami technologicznymi. Pozwoliło nam to przenieść 1:1 przetestowany program z symulacji do fizycznego układu – zaznacza Jarosław Strug.
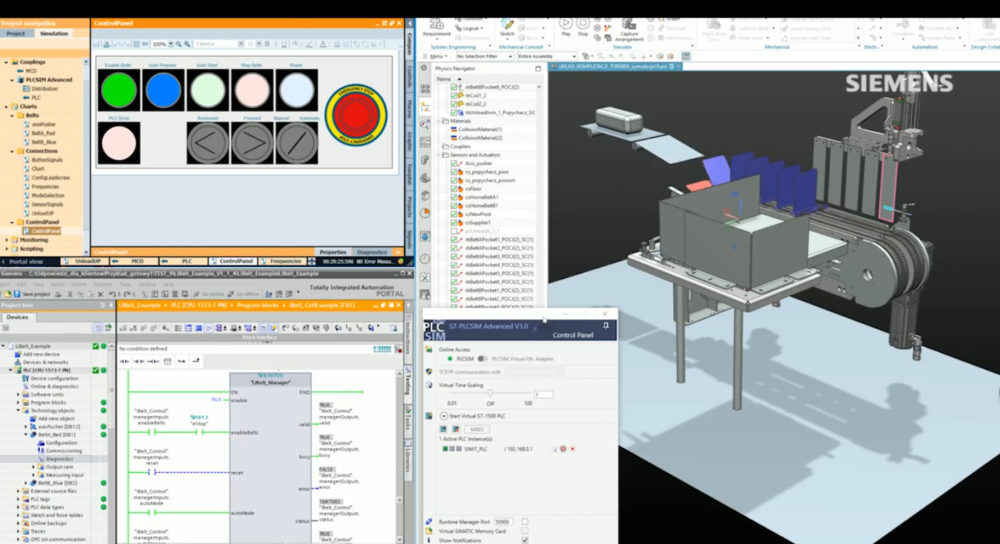
3 poziomy cyfrowych bliźniaków
Arkadiusz Rodak, ekspert ASTOR-a ds. przemysłu 4.0, podczas spotkania organizowanego przez krakowski Hub Innowacji Cyfrowych hub4industry, wyjaśniał, że opracowywane modele są zależne od potrzeb firm i da się wyróżnić 3 stopnie rozwiązania. Pierwszym jest cyfrowy bliźniak zasobu, np. maszyny, drugim – digital twin procesu ze wszystkimi urządzeniami, które biorą w nim udział, z kolei trzeci obejmuje cyfrowe odwzorowanie biznesu. Samą koncepcję technologii, jej powstanie i przykłady wykorzystania, np. przez miasta czy firmy produkcyjne z branży kosmicznej i motoryzacyjnej, opisywaliśmy w artykule pt. „Wszystko zostanie skopiowane – digital twin w fabryce„.