Niemiecki koncern przygotował tłoki do silnika modelu 911 GT2 RS na drukarkach 3D we współpracy z Mahle i Trumpf. Koncepcją zajęła się pierwsza z firm, na co dzień wytwarzająca części samochodowe, i wykorzystała tzw. projekt bioniczny naśladujący naturalne struktury (np. ludzki szkielet). Celem było opracowanie elementu w taki sposób, by ilość materiału w poszczególnych miejscach była dostosowana do późniejszego obciążenia elementu. W konsekwencji waga tłoku ma zmniejszyć się o około 20% przy jednoczesnym zwiększeniu sztywności. Nowa konstrukcja obejmuje też specjalnie ukształtowany kanał chłodzący, który obniża temperaturę i umożliwia pracę silnika z wyższą prędkością obrotową. Konstruktorzy użyli stopu aluminium, który do tej pory firma Mahle stosowała w przypadku tłoków odlewanych.
Testy obciążeniowe
Wydruk przygotował Trumpf, przedsiębiorstwo produkujące narzędzia do przetwarzania metali i obróbki laserowej. Tłok wytworzony w 3D składa się 12 tysięcy warstw aluminiowego proszku, spiekanych w technologii Laser Metal Fusion. Czas powstania jednego tłoka to około 12 godzin, po wydrukowaniu część jest wygładzana i poddawana próbom wytrzymałościowym symulującym obciążenia eksploatacyjne. Inżynierowie sprawdzili element także techniką tomografii komputerowej, trójwymiarowym skanem oraz za pomocą mikroskopu. Następnie sześć sztuk zamontowali w silniku Porsche 911 GT2 RS, który pomyślnie przepracował 200 godzin – m.in. 135 godzin przy pełnym obciążeniu i symulacyjny ekwiwalent 6 tys. km ze średnią prędkością 250 km/h (z przerwami na tankowanie).
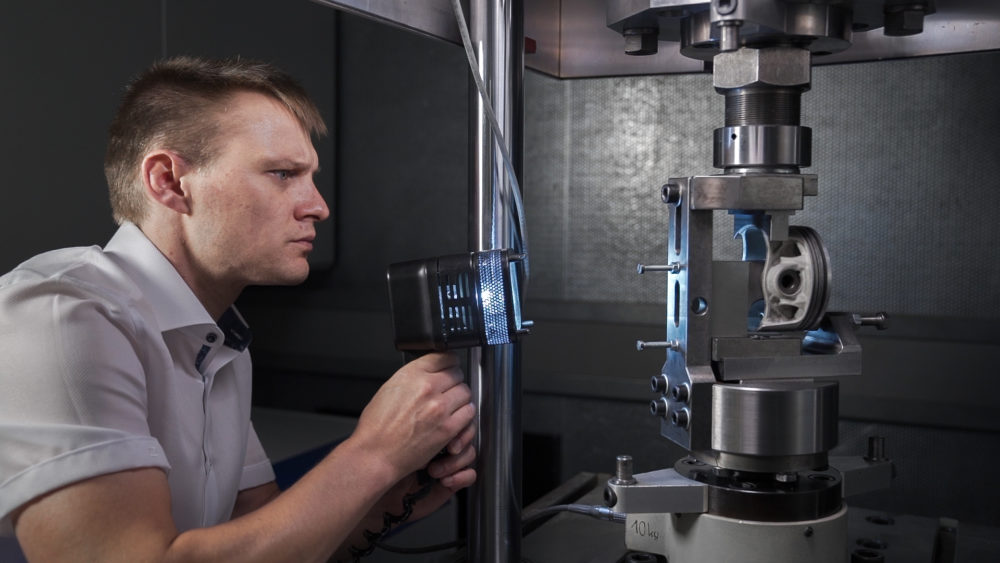
LMF, czyli SLM
Technologia LMF, jak ją określa Trumpf, wykorzystywana do produkcji nowych tłoków Porsche, to odpowiednik Selective Laser Melting, czyli selektywnego stapiania wiązką metali – SLM opisała szczegółowo w naszym serwisie Kinga Skrzek. Grubość pojedynczej warstwy w Selective Laser Melting to 0,1 mm, co zapewnia powtarzalność drukowanych elementów nawet przy bardzo złożonej geometrii. Tę technologię najczęściej stosują firmy z branży lotniczej, a także centra serwisowe drukujące narzędzia lub części zamienne. SLM, obok Laser-directed Energy Deposition, wykorzystali również badacze pracujący nad reaktorem jądrowym drukowanym w 3D.