SaMASZ jest producentem przeszło 300 modeli maszyn rolniczych oraz komunalnych, m.in. kosiarek dyskowych, bębnowych, przetrząsaczy, zgrabiarek, wozów paszowych, ramion wysięgnikowych, kosiarek bijakowych, głowic roboczych i pługów odśnieżnych. W 2018 roku firma zmieniła siedzię – z Białegostoku na Zabłudów. Obecnie, w kompleksie o powierzchni 13 hektarów, których 2,6 zajmuje główna hala produkcyjna, przedsiębiorstwo zatrudnia blisko tysiąc osób. Równocześnie z otwarciem nowej fabryki, SaMASZ uruchomił zautomatyzowaną malarnię kataforetyczną (KTL) i proszkową. Malarnia składa się z 4 głównych procesów, czyli mechanicznego, a następnie chemicznego przygotowania powierzchni, malowania kataforetycznego i proszkowego.
Z czego składa się zautomatyzowana malarnia?
Procesy są przeprowadzane z wykorzystaniem dwóch wind załadowczych, automatycznej śrutownicy, a także systemu 13 wanien z kąpielami zanurzeniowymi, który obejmuje chemiczne przygotowanie powierzchni oraz malowanie kataforetyczne. Z kolei nad wannami są 3 zautomatyzowane portale załadowczo–rozładowcze. Następnie elementy trafiają do suszarki KTL i buforów chłodzenia przed kabinami proszkowymi. Kolejne są: strefa z dwoma gniazdami malowania proszkowego: automatyczna kabina firmy GEMA oraz kabina do malowania ręcznego marki GWOMAL, piec do polimeryzacji proszku, bufor oraz strefa rozładunku detali za pomocą 2 wind rozładowczych, a także systemem transportu podwieszanego Power&Free o długości 1026 m.
Malarnią zarządza centralna jednostka sterująca z wyznaczonym 6-minutowym taktem linii. Maksymalne wymiary detalu jaki obsługuje linia, to: 2 metry wysokości, 1 metr szerokości i 4,5 metra długości.
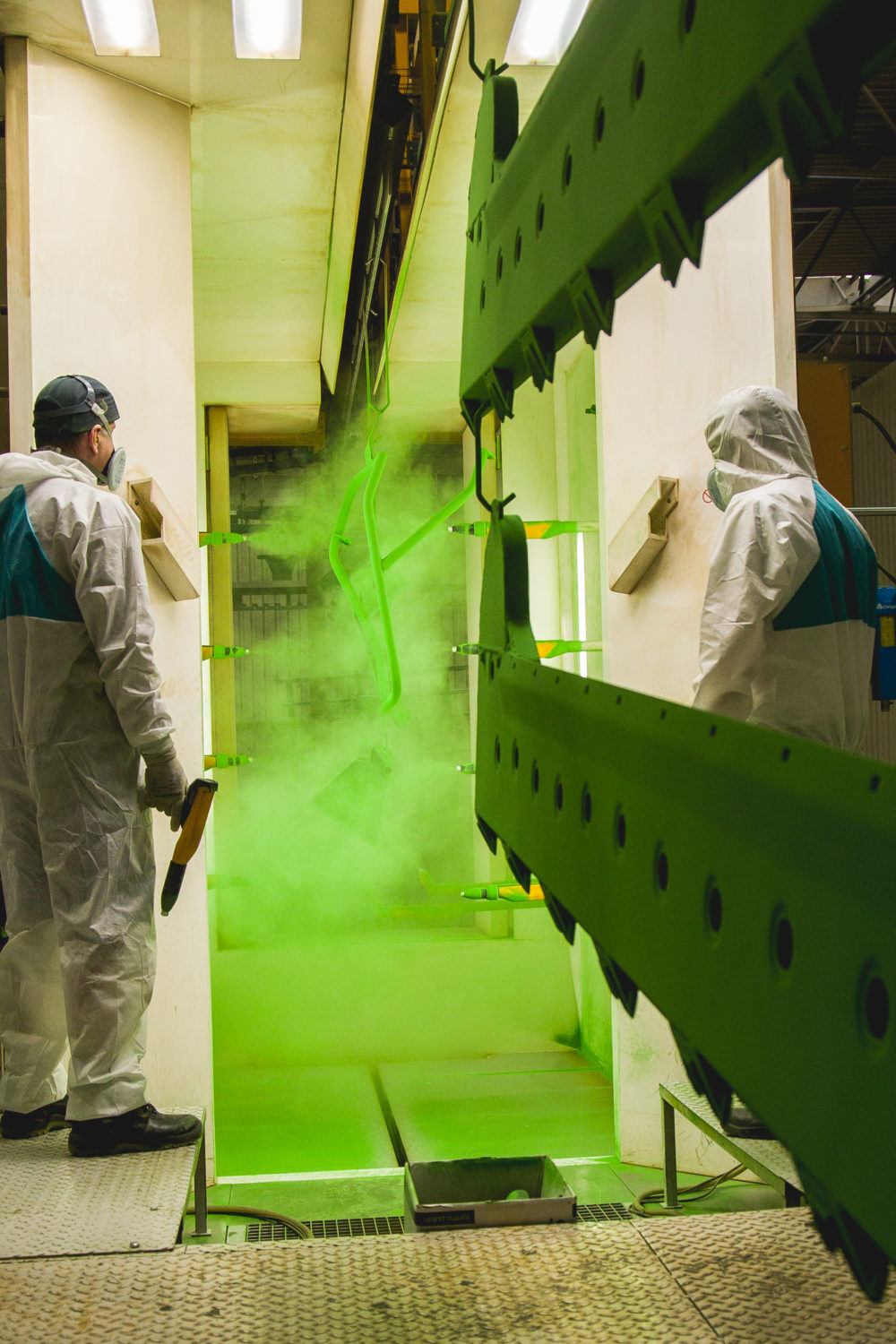
Wykonawca
Automatyczną linię malarską zaprojektowała i wykonała polska firma ADAL – producent urządzeń i instalacji wykorzystywanych w inżynierii powierzchni, systemów transportu technologicznego oraz urządzeń do montażu węży wysokociśnieniowych. Automatyczną śrutownicę dostarczyła firma Wheelabrator, a kabinę malarską dostarczyła firma P.C. Systems – przedstawiciel przedsiębiorstwa Gema Switzerland.
Powód wdrożenia
Leszek Szulc, dyrektor Działu Technicznego i Produkcji SaMASZ, wyjaśnia, że malowanie proszkowe jest jedną z efektywniejszych metod pokrywania metali:
– Farby proszkowe są trwalsze i estetyczniejsze w porównaniu z tradycyjną metodą pokrywania powierzchni przy użyciu lakierów ciekłych. Zapewniają zdecydowanie większą ochronę antykorozyjną oraz wysoką odporność na działanie czynników zewnętrznych. Są też w pełni bezpieczne dla ludzi i środowiska ze względu na brak w ich składzie rozpuszczalników.
Lakiernia, poza ochroną przed niszczeniem materiałów, a także promieniowaniem UV, wpływa też na wydajność całego procesu w SaMASZ. Kolejnym istotnym aspektem jest automatyzacja kabiny proszkowej, gdzie elektrostatyczne pistolety proszkowe oraz system z panelem operatorskim umożliwiają lepsze zarządzanie materiałem do malowania, a także szybką i bezpyłową zmianę używanej barwy.
– To dla nas bardzo ważne, ponieważ w ofercie mamy ponad 300 różnych produktów malowanych w różnych kolorach. Warto zaznaczyć, iż SaMASZ jednego dnia produkuje zarówno kosiarki bębnowe, dyskowe, przetrząsacze, zgrabiarki, jak i maszyny komunalne w różnych konfiguracjach kolorystycznych.
Etapy procesu malowania
Cały proces malowania rozpoczyna się od mechanicznego przygotowania powierzchni w automatycznej śrutownicy wpiętej we wspomniany transport elementów P&F. Śrutownica ma 12 turbin (każda o mocy 11 kW), które umożliwiają strumieniową obróbkę transportowanych elementów. Dzięki temu powstaje jednolita struktura oraz usuwane są zanieczyszczenia z powierzchni materiału. Detale do procesu obróbki strumieniowo-ściernej są zawieszane na windach załadunkowych i po śrutowaniu przewożone do obszaru chemicznego przygotowania powierzchni.
Chemiczne przygotowanie powierzchni ma miejsce w 9-wannowej myjce taktowej obsługiwanej za pomocą trzech zautomatyzowanych portali jezdnych. Odpowiedzialne są one za przenoszenie trawersów [poprzecznych belek z kilkoma punktami podwieszenia – red.] w obszarze wanien. W pierwszej wannie jest prowadzone natryskowe odtłuszczanie alkaliczne, a następnie trawers z detalami jest przenoszony do kolejnej wanny, gdzie następuje zanurzeniowe odtłuszczanie alkaliczne. Obie wanny odpowiadają za oczyszczanie detali oraz wypłukiwanie cząstek zanieczyszczeń, pozostałych po obróbce ściernej. Temperatura kąpieli oscyluje w przedziale 45-50°C.
Po zakończonym cyklu, na elementach można zauważyć delikatny ciągły film wodny, który świadczy o prawidłowym odtłuszczeniu. W kolejnych zbiornikach części są płukane w wodzie sieciowej (krążącej w sieci grzewczej). Podczas wynurzenia elementy zostają dodatkowo spryskane świeżą wodą, żeby je zwilżyć i zapobiec przesychaniu między kolejnymi kąpielami. W szóstej wannie przebiega kąpiel aktywacyjna, która przygotowuje powierzchnię do nałożenia drobnokrystalicznej, jednorodnej powłoki fosforanu cynku. Stosowany preparat po rozpuszczeniu w wodzie zdemineralizowanej powoduje powstawanie wielu zarodków krystalizacji, co w dalszym etapie obróbki (fosforanowaniu) prowadzi do powstania szczelnej powłoki. Wanna siódma odpowiada właśnie za fosforanowanie cynkowe. Podczas najważniejszego procesu kąpieli następuje trawienie powierzchni materiału, a na tak przygotowanym podłożu tworzy się powłoka fosforanu cynku. Proces fosforanowania zachodzi w temperaturze 43-48°C.
W dwóch ostatnich zbiornikach z obszaru przygotowania powierzchni elementy są opłukiwane wodą sieciową i demineralizowaną. Bardzo istotne jest, by ta druga miała przewodność nieprzekraczającą 30 µS/cm (mikrosimens na centymetr), co daje pewność, że detale są prawidłowo przygotowane do malowania powłoką antykorozyjną KTL.
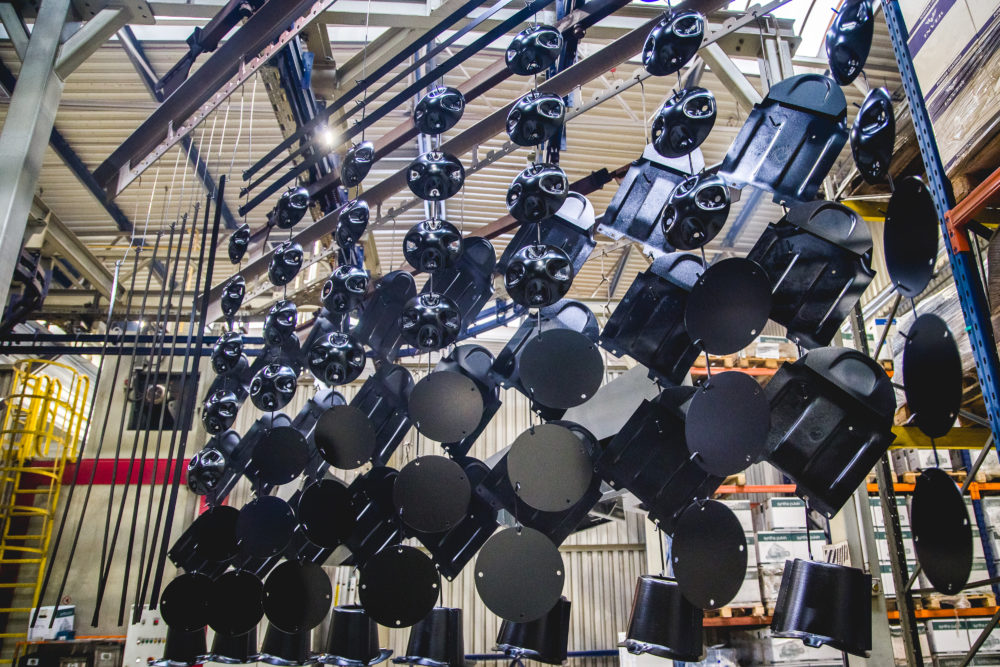
Malowanie kataforetyczne
W tej fazie procesu wykorzystywane są 4 wanny. W pierwszej następuje malowanie kataforetyczne, tzn. na zanurzone detale jest nanoszona antykorozyjna powłoka. W wodzie zdemineralizowanej używanej do kąpieli rozpuszczone są główne składniki farby – pasta CP458D zawierająca pigment oraz emulsja P6200HE zawierająca spoiwo farby.
Ilość pasty i spoiwa powinna być utrzymywana na poziomie 15-17%, a temperatura farby musi mieć stałą wartość 34-35oC. Dodatkowo farba jest poddawana stałej cyrkulacji, żeby zapobiec sedymentacji, a tym samym – zniszczenia farby. Po zanurzeniu detali przykładane jest napięcie stałe z przedziału 220-270 V co powoduje równomierne rozłożenie farby. Wraz ze wzrostem napięcia wzrasta grubość gotowej powłoki w zakresie 5-40 µm. Pozostałe 3 wanny są odpowiedzialne za ultrafiltrację – podstawową część procesu malowania kataforetycznego.
Główną rolą ultrafiltracji jest kontrola poziomu zanieczyszczeń kąpieli rozpuszczalnikami i odzysk stałych cząstek farby, które nie zostały przyciągnięte do wyrobów podczas malowania. Do wytwarzania ultrafiltratu używamy układu 2 membran, przez które nieustannie przepływa farba KTL pobierana z pierwszego zbiornika. Proces płukania detali w każdej z wanien jest zakończony natryskiem świeżą wodą/ultrafiltratem, po czym detal opuszcza strefę i trafia do pieca wygrzewania powłoki KTL. Po wygrzaniu detale trafiają do kolejki do malowania proszkowego.
Zastosowanie kabiny i aplikacji firmy Gema zapewnia automatyzację całego procesu. Kabina ma 12 automatycznych pistoletów proszkowych rozmieszczonych na trzech pionowych manipulatorach oraz 2 pistolety proszkowe ręczne obsługiwane przez malarzy. Wjeżdżając do kabiny, detale skanowane są za pomocą bramki świetlnej, która dostarcza sterownikowi informację o ich kształcie. Dzięki temu manipulatory zachowują odpowiednią odległość końcówki od malowanego przedmiotu, co prowadzi do równomiernego krycia powierzchni. Po naniesieniu farby przez manipulator malarze zajmują się trudnodostępnymi miejscami.
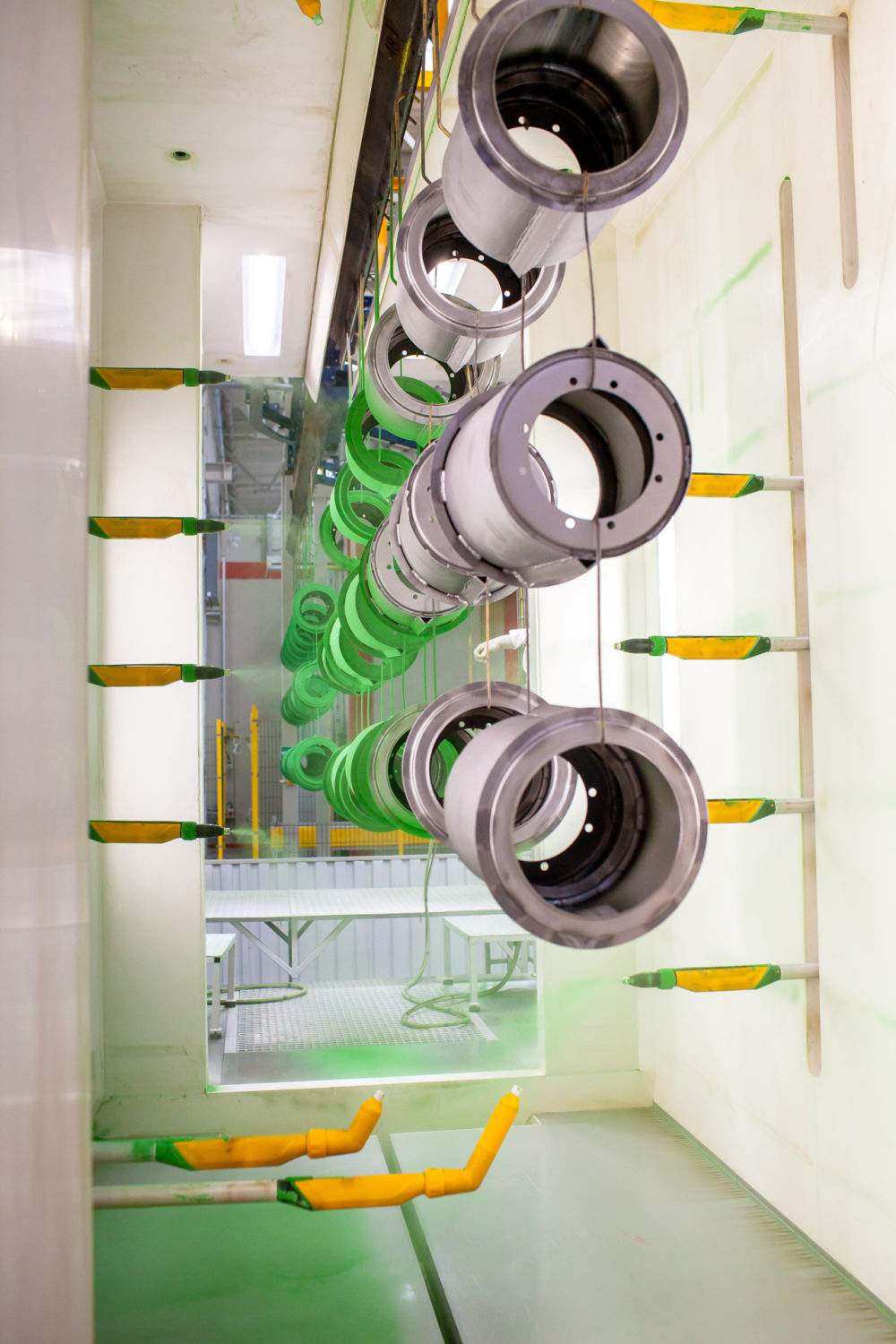
Kolejną zaletą kabiny jest szybka zmiana kolorów. Konstrukcja zbudowana z PVC i zastosowanie dysz czyszczących sprawia, że proszek w bardzo małym stopniu osiada wewnątrz kabiny, co przy szybkiej zmianie barwy jest niezwykle istotne. Nowa kabina ma też system odzyskiwania proszku, przez co zużywamy mniej farby i oszczędzamy pieniądze. Rozwiązania przedsiębiorstwa Gema prowadzą też do bardziej ekonomicznego napylania farby, co przy starej linii było trudne do osiągnięcia. Jeśli chodzi o bezpieczeństwo, w razie powstania ognia, cała malarnia zostaje wyłączona, a gaz CO2 zostaje wtłoczony do systemu wyciągowego kabiny.
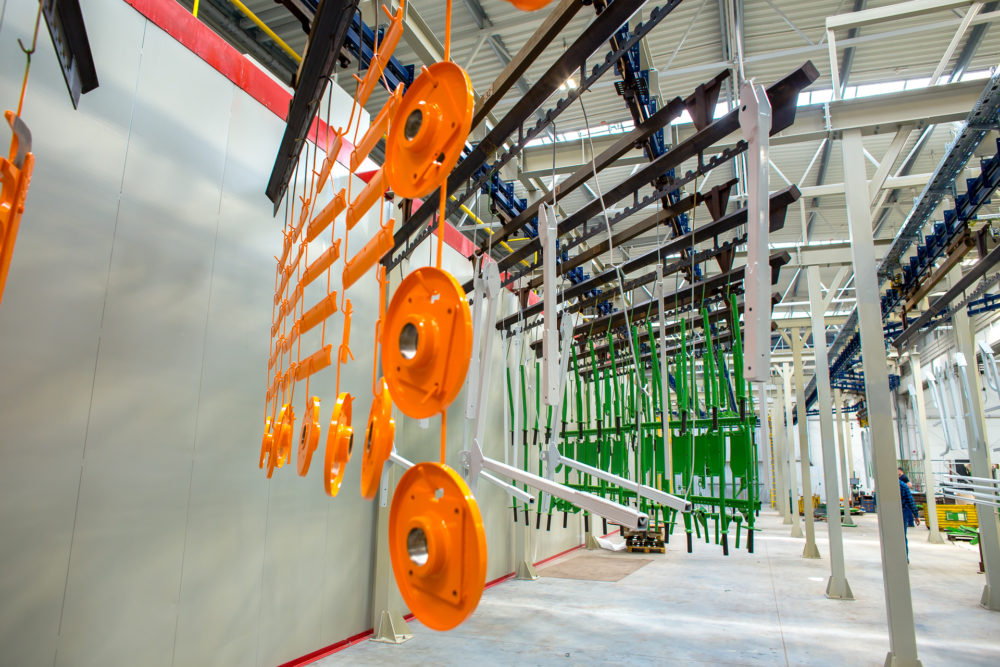
Założeniem przyjętym już na etapie projektowania było podwojenie wydajności malarni i jednoczesne potrojenie jakości w porównaniu do starego zakładu. To wynikało z planów ciągłego poszerzenia gamy produktów oraz ekspansji na nowe rynki. Dzięki zastosowanym instalacjom i zautomatyzowaniu procesu na poszczególnych etapach jest on powtarzalny i w pełni kontrolowany.
Automatyzacja malowania proszkowego daje wysoką efektywność produkcji, przy zachowanych parametrach jakościowych. Z kolei zapewnienie powtarzalności procesu przekłada się na ograniczenie błędów podczas obróbki lakierniczej. Maszyny SaMASZ muszą często działać w trudnych warunkach środowiskowych, stąd konieczność spełniania norm antykorozyjnych. Dzięki automatyzacji całej linii malarskiej możliwe jest monitorowanie procesu i w razie awarii lub nagłych sytuacji, skuteczne i szybkie reagowanie.