Michał Lach, kierownik utrzymania ruchu w Stellantis: W zakładzie w Tychach zajmujemy się produkcją samochodów marek Fiat, Abarth i Lancia. Ostatnio swoją obecność na rynku zaznaczyliśmy dzięki wyprodukowaniu 2,5-milionowego modelu Fiata 500. Dzisiaj pokażę, jak wdrażamy automatyzację i wybieramy miejsca oraz obciążające procesy, które warto usprawniać. Działamy w zakresie World Class Manufacturing, czyli systemu zarządzania umożliwiającego analizę kosztów, stratyfikację i wskazanie interesujących nas działań z zakresu automatyzacji. Określamy obszar modelowy do eliminacji strat, oceniamy koszty, jakie musimy ponieść przy automatyzacji i zyski wynikające z nowego rozwiązania.
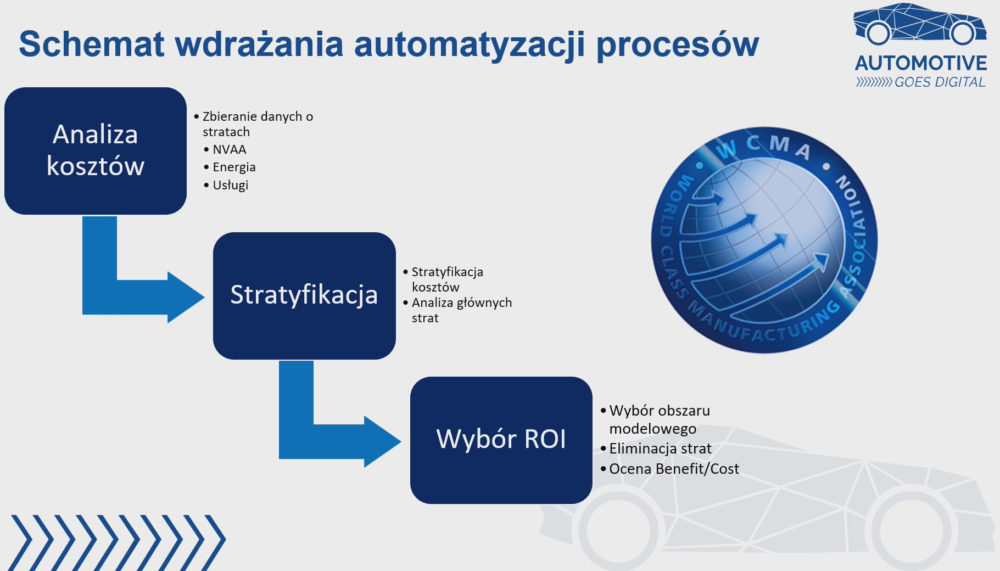
World Class Manufacturing
W WCM, czyli Produkcji Klasy Światowej, chodzi o doskonalenie wytwarzania i osiągnięcie jak najwyższej ilości przy jednoczesnemu sprostaniu założeniom jakościowym, a także dążenie do zera: strat, awarii, wypadków i defektów. WCM kładzie nacisk na ciągłe podnoszenie kompetencji i poszerzanie wiedzy załogi.
Metoda opiera się na kilku koncepcjach, są to m.in.:
- Just in Time polegająca na eliminowaniu marnotrawstwa m.in. dzięki temu, że właściwa liczba części potrzebnych do procesu zostanie dostarczona we właściwym czasie
- Total Quality Control, czyli ciągłe wykrywanie, ograniczanie i eliminowanie błędów w produkcji, rozwój pracowników, udoskonalanie łańcucha dostaw oraz doświadczeń klienta
- Total Productive Maintenance, czyli zapewnianie jak najwyższej efektywności maszyn poprzez maksymalne wykorzystanie czasu ich pracy
- Total Industrial Engineering, tj. zwiększanie wydajności pracy poprzez redukcję tzw. Muda, Mura i Muri – marnotrawstwa, nieregularności oraz nadmiernego obciążenia.
Poszukiwanie rozwiązań
Po wyborze obszaru modelowego pracujemy zespołowo, co niejednokrotnie prowadzi nas do finału, tj. usprawnienia danego działania, poprzez różne metody zarządzania projektami i poszukiwania rozwiązań. Sposobów działania jest wiele, dlatego stosując je, skupiamy się na kilku kluczowych kwestiach: ergonomii, bezpieczeństwie, poprawie pracy na danym stanowisku, ulepszeniach produktu i funkcjonowania maszyn. Dzięki temu metody prowadzą nas do jednego, konkretnego rozwiązania.
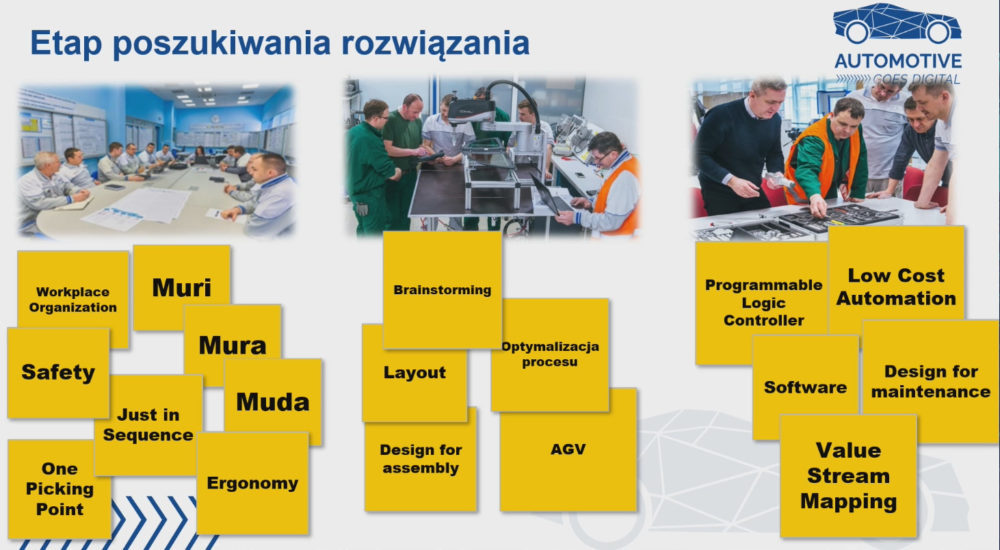
3 sposoby wdrażania automatyzacji
Jeżeli chodzi o wdrażanie automatyzacji, to w tej chwili możemy powiedzieć, że mamy 3 różne sposoby. Pierwszy sprowadza się do wyboru profesjonalnego integratora, szczególnie wtedy, kiedy wpływ na produkt, czyli samochody, a także na produkcję, jest bardzo duży. Jeśli chodzi o drugą metodę, to polega ona na naszym wejściu w interakcję z integratorem. Pomagamy wykonywać najprostsze czynności, co przekłada się na znaczną redukcję kosztów. W ostatnim trybie chodzi o samodzielne wykonywanie prostej automatyzacji, co jest dla nas satysfakcjonujące. Zaprezentuję, jak przygotowaliśmy warunki do takich działań i jedno z obecnie wdrażanych rozwiązań.
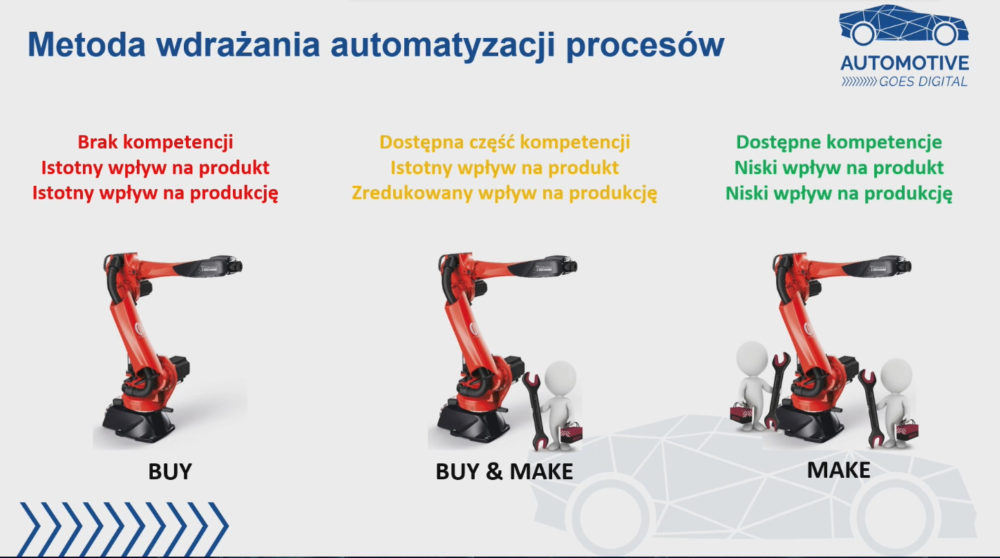
Kooperacja z firmami
W zakresie współpracy z firmami staramy się działać z organizacjami pobliskimi, czego przykładem jest SEW Eurodrive – przedsiębiorstwo, które dostarczyło nam wszystkie komponenty do wózka AGV [automated guided vehicle – red.] umiejącego przewozić ładunki o masie 1500 kilogramów. Dzięki temu, na podstawie rozwiązania Max Solution, powstał nowy transporter. Po naszej stronie było zbudowanie wszystkich konstrukcji mechanicznych, zagwarantowanie pól odkładczych [miejsc załadunku u rozładunku detali – red.], oprogramowanie sterowników nadrzędnych, parametryzacja bezpieczeństwa, dzięki czemu sporo się nauczyliśmy. Wśród działań SEW było przygotowanie deklaracji zgodności na podstawie tego, co udało nam się wypracować.
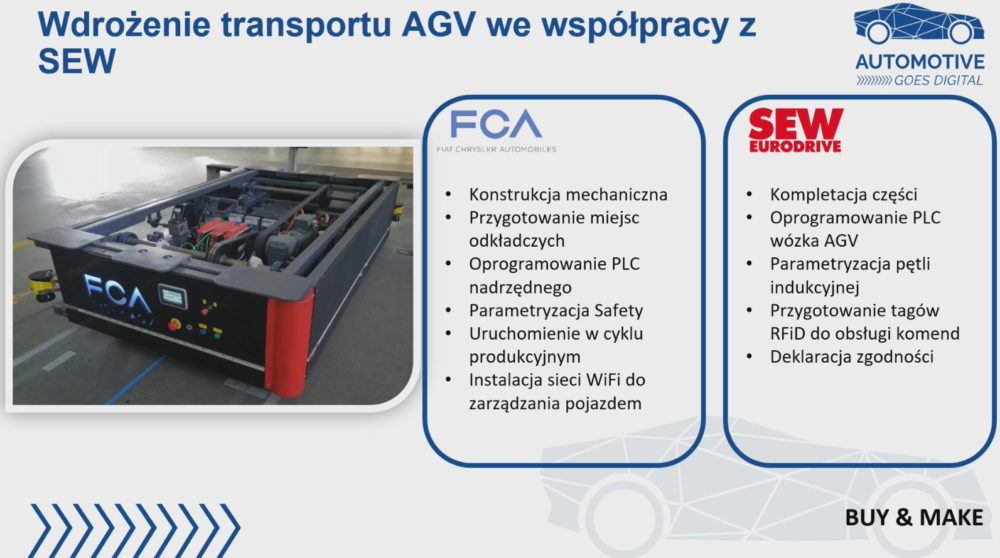
Kolejnym rozwiązaniem przygotowanym we współpracy z inną firmą i wpisującym się w obecne trendy automatyzacji, jest zrobotyzowana stacja nakładania primera przygotowana z firmą RBS Robotics. W tym przypadku wykorzystaliśmy część sprzętu przechowywanego w naszym magazynie, tj. 2 roboty C5G i stoły centrujące, które pamiętają czasy Fiata Pandy. W ten sposób znacznie ograniczyliśmy wydatki na tę inwestycję.
RBS Robotics, na bazie przekazanych przez nas urządzeń, zaprojektowało dla nas stację i przygotowało symulacje, co było podstawą do naszych działań, czyli mechanicznego montażu, wykonania podłączeń elektrycznych i wykończenia budowy stacji. Obecnie jesteśmy na etapie weryfikacji programów robotów, schematów elektrycznych i deklaracji zgodności. Mam nadzieję, że w najbliższym czasie pochwalimy się działającą stacją.
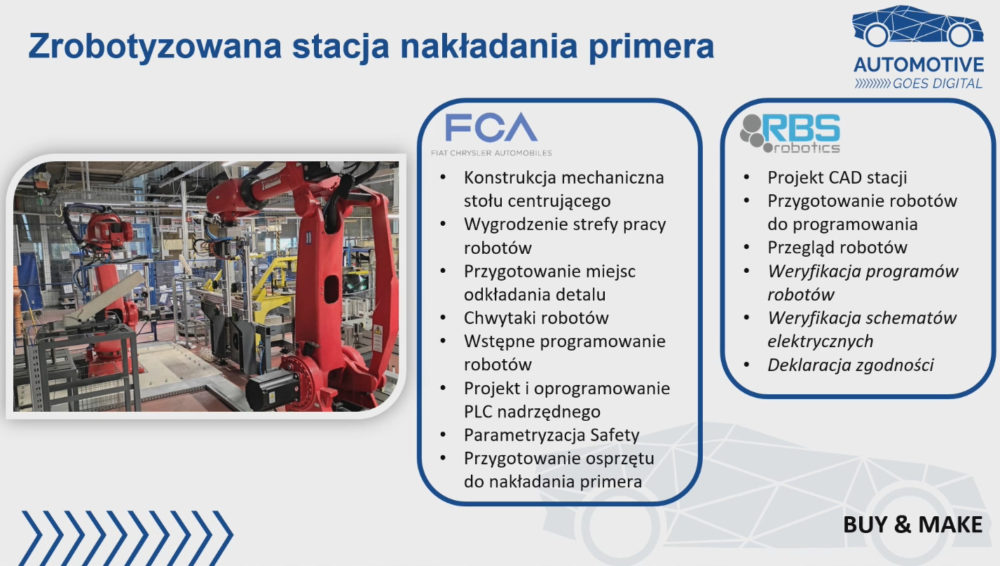
Zakup rozwiązań – predykcyjne utrzymanie ruchu
W przedsiębiorstwie mamy również takie procesy, których wpływ na wytwarzanie produktów jest pośredni – jednym z przykładów jest utrzymanie ruchu. W tym przypadku Siemens wyszedł nam naprzeciw, oferując rozwiązanie chmurowe Mindsphere i wybierając firmę IT9 z inkubatora Spark 2.0. IT9 przygotuje aplikację pomagającą nam rozpoznawać nieprawidłowości w działaniu urządzenia do nakładania kleju.
Możemy powiedzieć, że w normalnym działaniu takiej maszyny, jak robot do nakładania kleju, zawsze istnieje szansa wystąpienia jakiejś anomalii, która – nawet jeśli jest sygnalizowana alarmem – powoduje zatrzymania i ograniczenia produkcji. Wówczas analizujemy zebrane dane, przygotowujemy plan rozwiązania problemu i wdrażamy działania umożliwiające jak najszybszy powrót do normalnego funkcjonowania. W przypadku wszystkich tego typu maszyn staramy się zbierać i analizować informacje, a dzięki temu przygotowywać metody ułatwiające eliminowanie problemów.
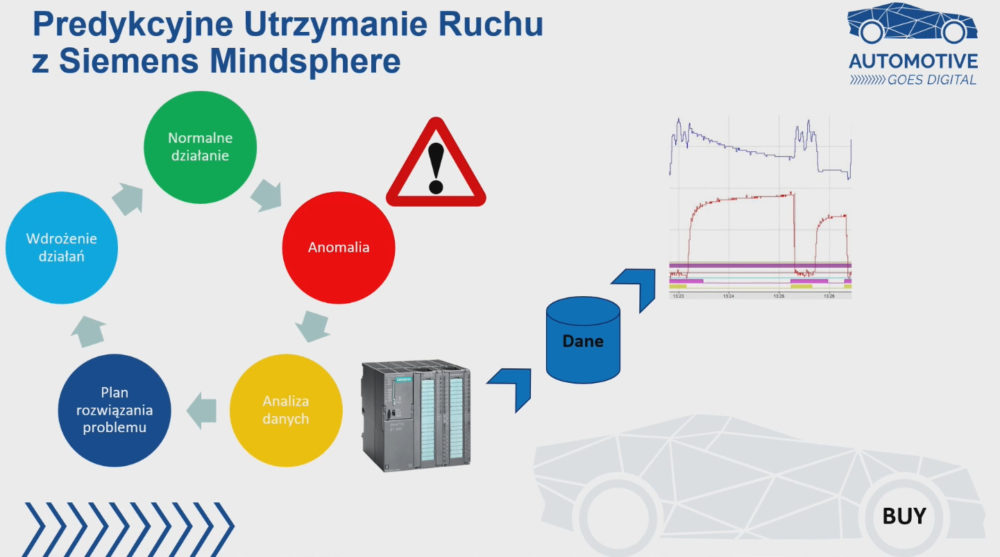
Jednak nas interesuje sytuacja, w której gromadzenie danych dzieje się online i trwa bez przerwy, a na podstawie już zebranych informacji i analizy ich, system uczy się, jak możemy zapobiegać problemom i reagować wcześniej. Dzięki takiemu rozwiązaniu bylibyśmy w stanie przeciwdziałać anomalii w funkcjonowaniu maszyny – zapobiec jej albo przynajmniej ją zaobserwować, jeśli miałaby się zdarzyć. Tak naprawdę tylko od nas zależy czy wykorzystamy wiedzę i czas, które zdobędziemy dzięki temu rozwiązaniu.
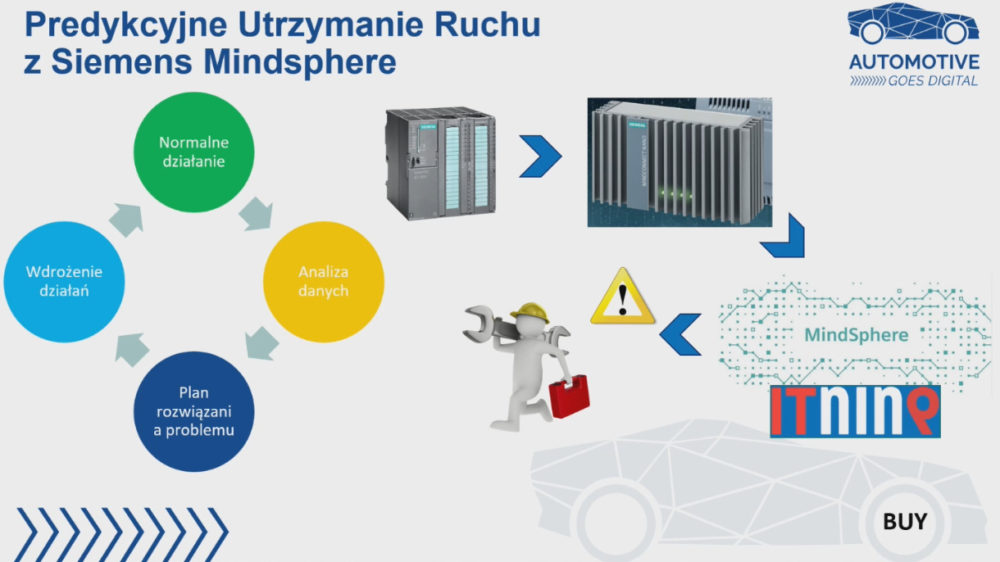
Low cost automation
Budowanie własnych rozwiązań automatyzacji rozpoczęło się od World Class Manufacturing i Low Cost Automation. Stworzona przez nas grupa osób wyłoniona spośród pracowników firmy, pozwoliła na stworzenie zespołu Kaizen Team, który od 10 lat zajmuje się tworzeniem różnorodnych rozwiązań ułatwiających zrealizowanie celów produkcyjnych.
Wybierając proces do automatyzacji, musieliśmy zacząć od wskazania człowieka, który będzie zarządzał działaniami. Kolejne kroki to wybór utalentowanych osób z produkcji, zaangażowanie menadżerów, pracowników produkcji i utrzymania ruchu. Myślę, że odnieśliśmy pewien sukces, co zobaczymy na następnym slajdzie. Obecnie działa około 450 zainstalowanych urządzeń, które wdrożył Kaizen Team.
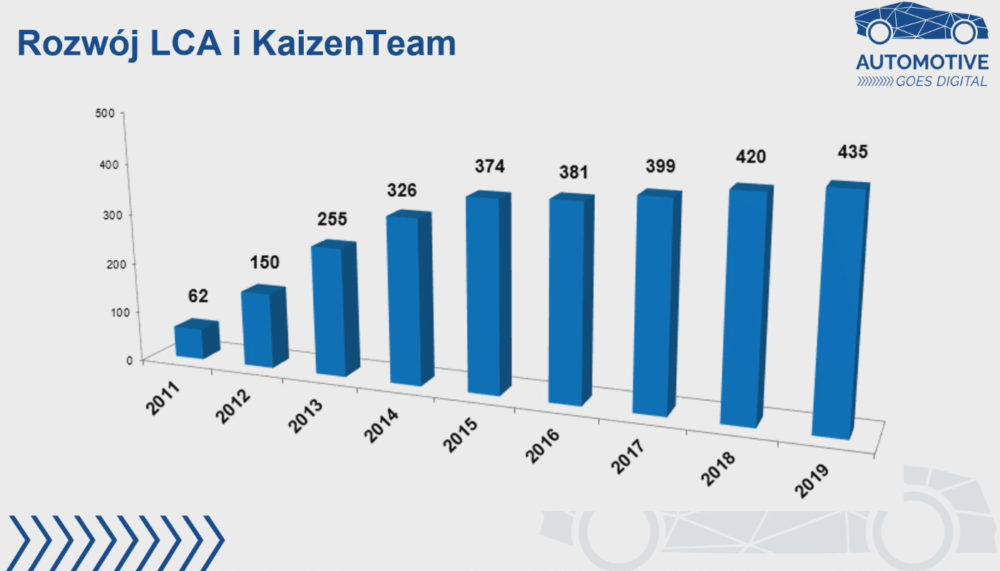
Wózek kittingowy
Teraz pokażę zautomatyzowany wózek kittingowy, czyli taki, który dostarcza detale do linii produkcyjnej. Konstrukcja jest w pełni autorska, wybraliśmy wszystkie elementy mechaniczne, elektryczne i elektroniczne. Zespół, który zajmuje się organizacją miejsc pracy, zaproponował nam, jakie detale transportować na wózku. Komponenty zbudowanego przez nas urządzenia nie obciążają magazynów części zamiennych, co wiąże się z redukcją kosztów. Przede wszystkim jednak dbamy o to, żeby osobie montującej elementy do samochodu było jak najłatwiej, żeby dostęp do detali był możliwie wygodny i żeby pracownik nie musiał wykonywać niepotrzebnych ruchów. Rozwiązanie jest bezpieczne, we współpracy z integratorami skupiamy się na przygotowaniu deklaracji zgodności, natomiast konstrukcję wykonujemy samodzielnie.
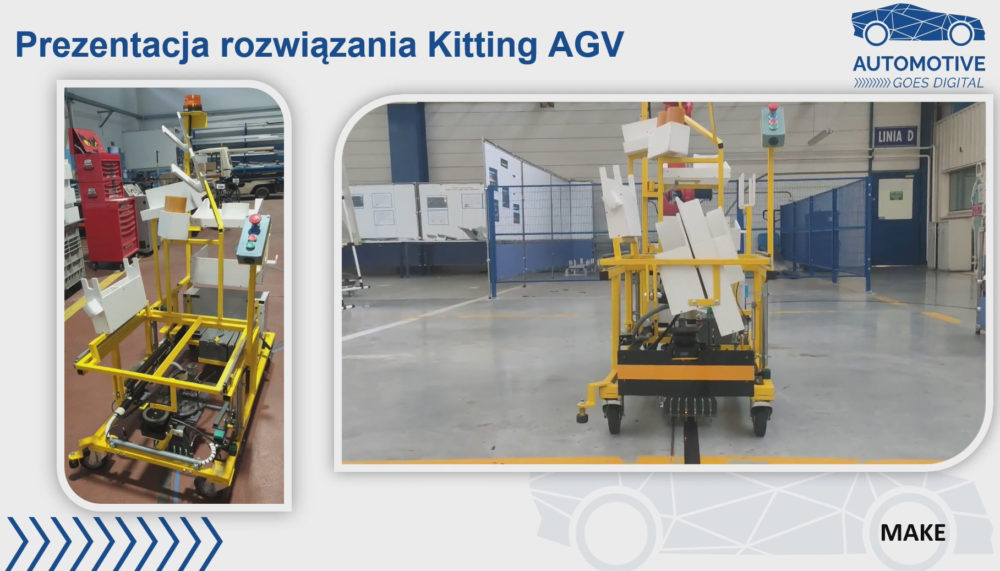
Nie tylko mniejsze koszty
Co możemy zyskać poza oszczędnościami? Na pewno rozwój kompetencji – to jedna z ważniejszych rzeczy, o którą dbamy. Szukając utalentowanych osób wśród pracowników produkcji, próbujemy ich przy okazji uczyć. Ci z większym doświadczeniem przekazują swoją wiedzę następnym – pokazują jak budować instalacje elektryczne, uczą projektowania schematów elektrycznych czy metod zabudowy szafy elektrycznej. Ćwiczymy poprzez wielokrotną budowę tych samych urządzeń. Na przykład wózków kittingowych powstało 25, więc jest to już tak naprawdę masowa produkcja. Trenujemy takie umiejętności, jak spawanie, standaryzujemy rozwiązania mechaniczne, unifikujemy całą elektronikę, a dzięki temu, że nie powiększamy stanu magazynowego, obniżamy koszty. Cały czas staramy się, żeby nasze rozwiązania były jak najbardziej bezpieczne i stosujemy najnowsze systemy ochrony.
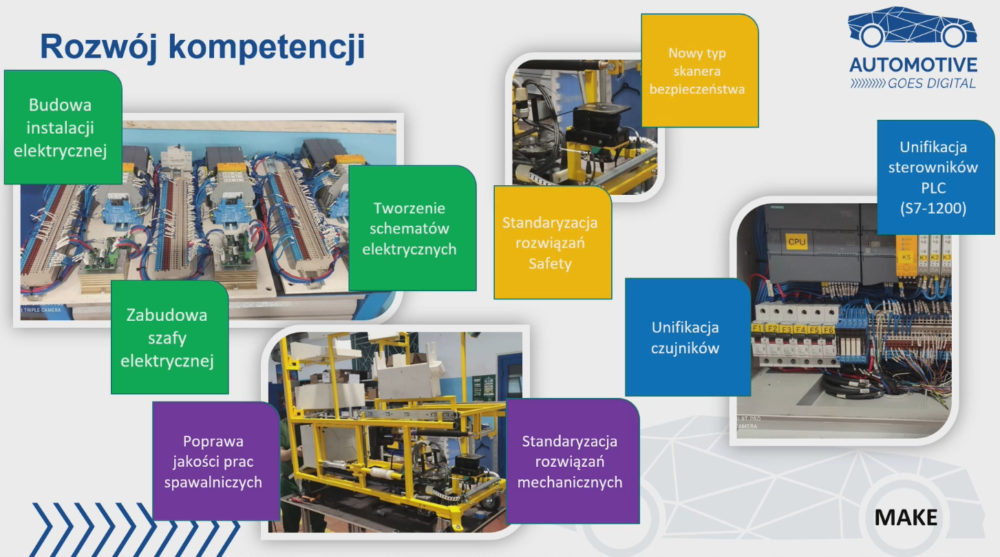
Szanse i zagrożenia
Działania, które podejmujemy, niosą za sobą zagrożenia i możliwości, o możliwościach już wspominałem, ale o zagrożeniach do tej pory nie mówiłem. Według mnie, bardzo często przy realizacji takich projektów pojawiają się trudności, które wynikają z braku wiedzy, jak długi czas wykonania, lub niejednokrotnie pojawiające się braki w dokumentacji, które później trzeba uzupełnić. Natomiast z drugiej strony niezaprzeczalnie obniżamy koszty automatyzacji, podnosimy poziom umiejętności i przygotowujemy pracowników Kaizen Teamu do późniejszej działalności w utrzymaniu ruchu. Dzięki temu, że sami budują urządzenia, to od razu skupiają się też na tym, co będą robili za parę lat, zajmując się ich obsługą w utrzymaniu ruchu. Obniżamy koszty również przez unifikację komponentów.
Słabe i mocne strony
Jeśli chodzi o słabe i mocne strony naszych rozwiązań, to problemem jest dla nas brak etapu projektowania CAD. Wszystkie opracowywane dotąd rozwiązania, tworzymy w czasie trwania projektu, kolejne działania tak naprawdę wymyślamy na bieżąco i budujemy na podstawie odręcznych szkiców. Stąd wynika ograniczona dokumentacja. Zredukowane czasy wdrożenia i obsługa, którą musimy świadczyć podczas uruchomienia, powodują skrócenie testów przed uruchomieniem, a to powoduje pojawienie się tzw. chorób wieku dziecięcego.
Wśród mocnych stron są mniejsze koszty i podnoszenie kwalifikacji, a także to, że w procesie projektowania angażujemy bardzo dużo działów. Wzrosło również znaczenie samodzielnego dokształcania się, niejednokrotnie nasi specjaliści są pionierami jeśli chodzi o stosowanie rozwiązań programistycznych bądź używanie nowych komponentów. Na własną rękę poszukujemy nowych technologii i robi to nie tylko utrzymanie ruchu, ale też produkcja.
Podsumowując, wspomnę o bardzo ważnych dla nas elementach – nasze podejście do automatyzacji pozwala szkolić pracowników działów technicznych, uczyć się budowy urządzeń dla utrzymania ruchu, a także unifikować komponenty przy zmniejszaniu kosztów. Dzięki wzrostowi kompetencji mamy lepszych i bardziej zaangażowanych pracowników, którzy chętnie podejmują wyzwania i jest też ważny aspekt, który buduje naszą wiedzę i daje nam kompetencje, dzięki którym rozumiemy, co chcemy osiągnąć i otrzymać. To sprawia, że lepiej pracuje nam się z integratorami.
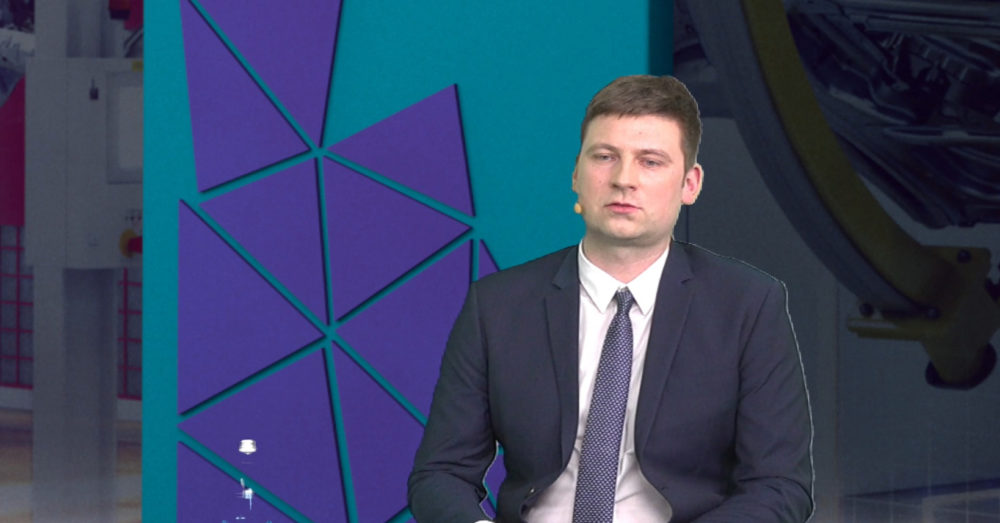
Stellantis to koncern motoryzacyjny, który pod swoim szyldem gromadzi 14 marek samochodów. Przedsiębiorstwo powstało w wyniku fuzji włosko-amerykańskiego Fiat Chrysler Automobiles i francuskiej Grupy PSA, przez co fabryki firmy działają na całym świecie. W Polsce m.in. w Gliwicach, Bielsku-Białej i Tychach. Tyski zakład ma 2,4 miliona metrów kwadratowych, z czego ponad jedna piąta to powierzchnia fabryki. W dziale spawania funkcjonuje 921 robotów, a nowe auta powstają co 73 sekundy. Na miejscu pracuje około 2400 osób, szkolących się m.in. w wirtualnej rzeczywistości. Fabryka wdraża procesy przyjazne środowisku – o 40% zmniejszyła zużycie energii, a o ponad połowę wody. Zmniejszyła też wytwarzanie odpadów – o 54%. Celem działań, jeśli chodzi o produkcję, jest 0 strat, wypadków, awarii i defektów.