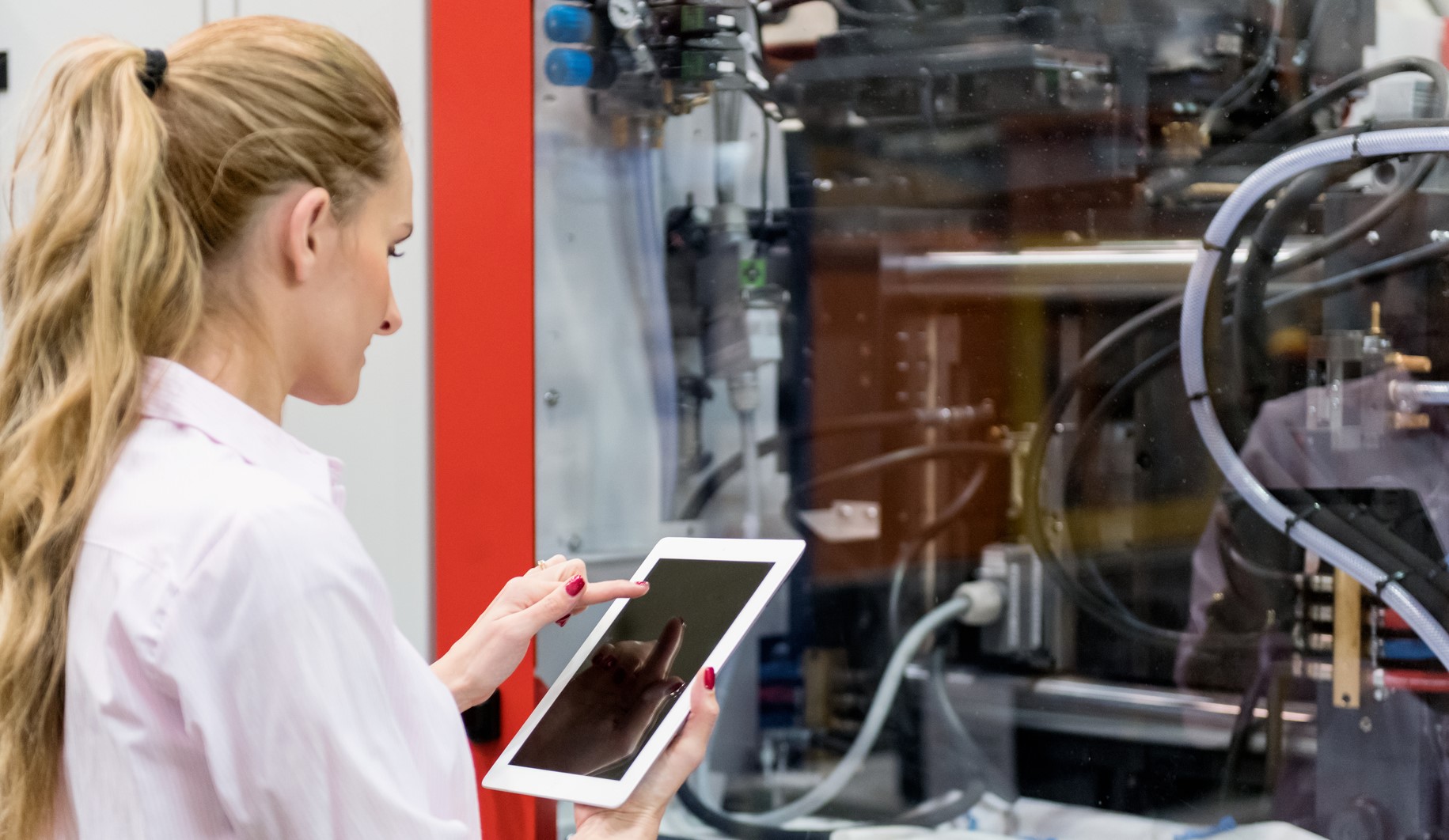
Zastosowanie technologii
Zastosowanie: S.C. Johnson Polska Sp. z o.o.
W zakładzie produkcyjnym S.C. Johnson Polska Sp. z o.o. informacje o problemach w realizacji planów produkcyjnych raportowano przy użyciu arkuszy papierowych. Osoby odpowiedzialne za rozwiązywanie problemów przekazywały pomiędzy sobą arkusze i omawiały je w trakcie spotkań organizacyjnych. Taki system zapewniał przepływ informacji, jednak efektywność i szybkość rozwiązywania problemów była niewystarczająca. Występował wysoki odsetek problemów nierozwiązanych oraz powtarzających się awarii. Zespół produkcyjny miał ograniczone możliwości zarządzania priorytetami i wiedzą – operatorzy skarżyli się na brak zwrotnej informacji o statusie awarii i podjętych działaniach naprawczych. Ręczny system raportowania nie pozwalał na dostatecznie szybkie angażowanie specjalistów i sprawne rozwiązywanie problemów. Nie pozwalał też na sprawne tworzenie i śledzenie statystyk przez kadrę menedżerską.
Wdrożono nowoczesny system rozwiązywania problemów – aplikację informatyczną, dostępną również na urządzeniach mobilnych. Wdrożony system – Bework udostępniono liderom produkcji oraz wszystkim pracownikom wsparcia produkcji. Kluczowi użytkownicy mogą korzystać z aplikacji codziennie, również zdalnie. Wprowadzono pełną automatyzację procesu rozwiązywania awarii, co przyczyniło się do poprawy efektywności zarządzania awariami. Skupiono się na lepszym zarządzaniu wiedzą i znacząco przyspieszono obieg informacji w całym zakładzie. Zwiększono zaangażowanie pracowników oraz poprawiono komfort i szybkość pracy wszystkich pracowników produkcji.
Dostępność i mobilność rozwiązania była fundamentalna dla szybkości podejmowania krytycznych decyzji w czasie COVID. W ciągu sześciu miesięcy od wprowadzenia systemu skrócono czas usuwania awarii o 30 %. Przekroczono wskaźnik 90% problemów na liniach produkcyjnych, które są skutecznie zamykane w ciągu tygodnia od wystąpienia, a ok. 97 % problemów udaje się rozwiązać w przeciągu 1 miesiąca od wystąpienia. Problemy przeterminowane zostały ograniczone do minimum. Zmienił się też charakter zgłoszeń: spadła liczba problemów związanych z zatrzymaniem produkcji na rzecz wzrostu zgłoszeń prewencyjnych, pomagających przeciwdziałać poważnym awariom. Rok do roku przyczyniło się to do zwiększenia efektywności wszystkich linii produkcyjnych średnio o 20%.
ul. Taśmowa 7, 02-677 Warszawa